Where cobots were once primarily known for their safety and ease of use, they are now transforming into autonomous systems capable of executing complex production tasks independently. The integration of vision technology and artificial intelligence marks a new era in industrial automation. WiredWorkers anticipates this with advanced solutions that go far beyond simple repeatability. This is the new reality of collaborative robotics.
From assistant to autonomous operating system
Cobots have rapidly evolved from programmable helpers into adaptive systems that make production processes smarter, safer, and more resilient. Their added value is no longer limited to relieving operators of simple pick-and-place tasks.
The latest generation of cobots includes:
- 2D/3D vision systems for real-time detection of shape, position, orientation, and size;
- AI algorithms to understand context, recognize deviations, and make decisions;
- Machine learning to optimize behavior based on feedback from previous executions.
In practice, this means a cobot that once relied on fixed templates and sequences can now independently locate, evaluate, and sort products—even with variation or unstructured input.
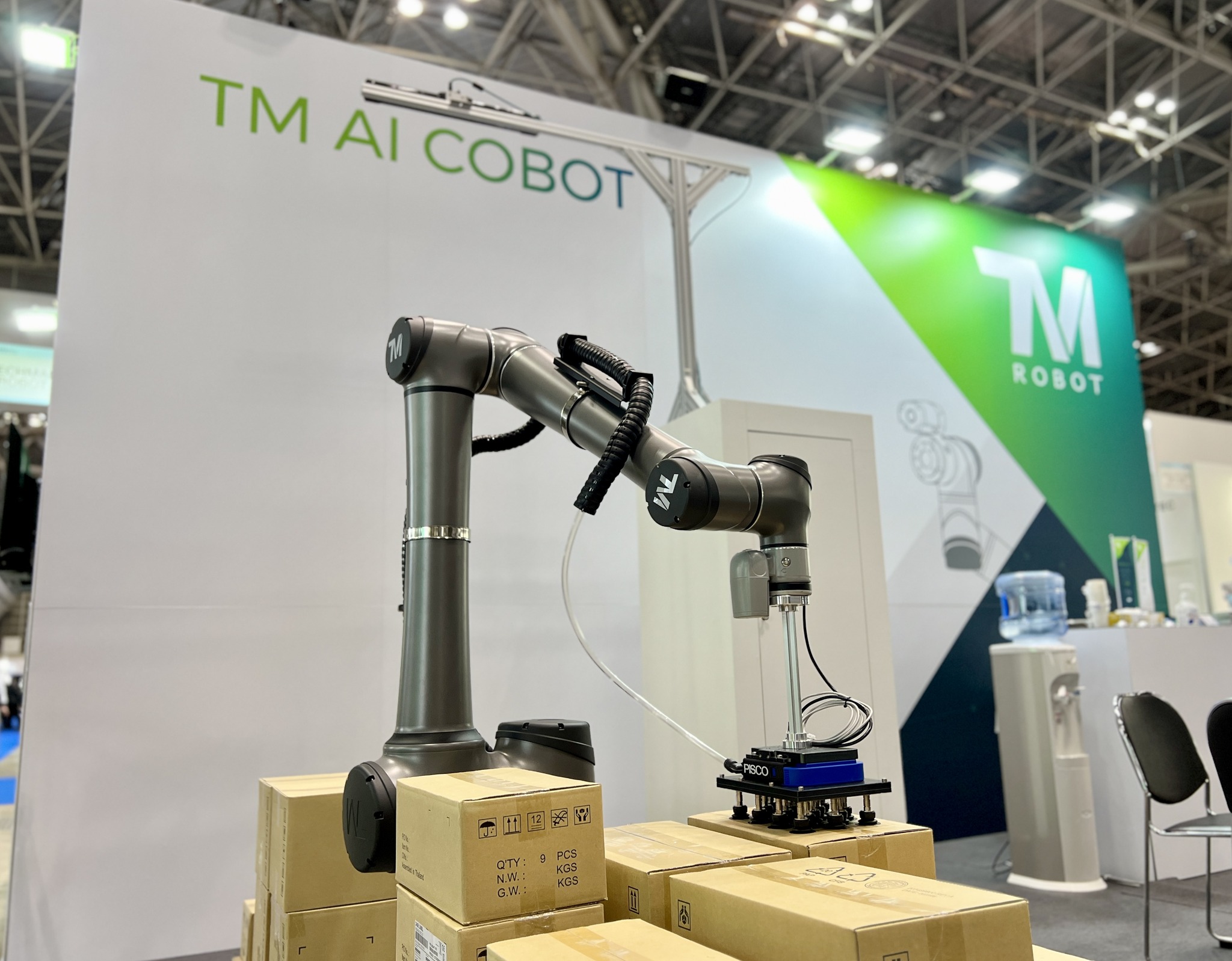
AI adds decision-making to perception
A vision system that recognizes objects is only the first step. The real value emerges when that data is also interpreted. That’s where AI comes in.
Imagine a cobot retrieving parts from a bin. Without AI, each product type must be trained separately. With AI, it can generalize: recognize new shapes, adjust its gripper angle, and choose the correct sequence.
Moreover, the system learns which decisions were most successful in the past—such as with challenging orientations or variant products—and adapts its behavior accordingly. This makes the cobot more robust in fluctuating processes.
Applications: from flexible sorting to inline quality control
AI and vision technology are not only suited to high-end industries; SMEs now benefit from this innovation as well. Some concrete applications include:
-
Flexible pick-and-place for variable product flows, such as in e-commerce or food packaging;
-
Assembly tasks involving tolerance recognition, such as fitting parts with minimal dimensional differences;
-
Inline quality control where deviations or defects are automatically detected and sorted out;
-
Assembly of customer-specific products, without requiring reprogramming for each variation.
Especially in sectors with high product variability and small batches, this offers significant benefits: reduced changeover time, higher first-time-right percentages, and less reliance on experienced operators.
Strategic value: agility in a changing world
The industrial context is evolving rapidly. Labor shortages, demand fluctuations, and the need for customization require flexibility. AI-driven cobots offer a strategic response.
They enable manufacturers to:
- Quickly switch between product variants without needing a programmer;
- Ensure quality and output even with unpredictable inputs;
- Reduce costs by working smarter, not harder;
- Adopt a future-proof production strategy that scales without relying on scarce technical personnel.
Investing in intelligent cobotics today means building a production infrastructure that can withstand tomorrow’s challenges.
Ready for the future
The use of AI and vision-enhanced cobots is not a technological gimmick—it’s a fundamental shift in how we approach production processes. Companies that embrace this technology are building smart, flexible factories where technology adapts to the process, not the other way around.
WiredWorkers is an expert in automation and has already helped several companies implement collaborative robots. Want to learn more about how to integrate cobots safely and efficiently? Contact us or schedule a free cobot consultation!