The rise of the collaborative robot (cobot) has made its way within the manufacturing industry and is now seen as a valuable tool for improving efficiency and productivity. While embraced within various industries, companies have also encountered a number of challenges when implementing a cobot. In this blog, we discuss some of the challenges and tips for making the implementation of a cobot as smooth as possible.
Challenges in cobot implementation
Safety and human-robot collaboration
One of the most pressing challenges is ensuring safe cooperation between cobots and human workers. Cobots are equipped by default with advanced safety sensors, such as force and touch detection to prevent collisions. But sometimes additional measures are needed. Defining clear work areas and training employees to work safely with cobots are also important aspects of this challenge.
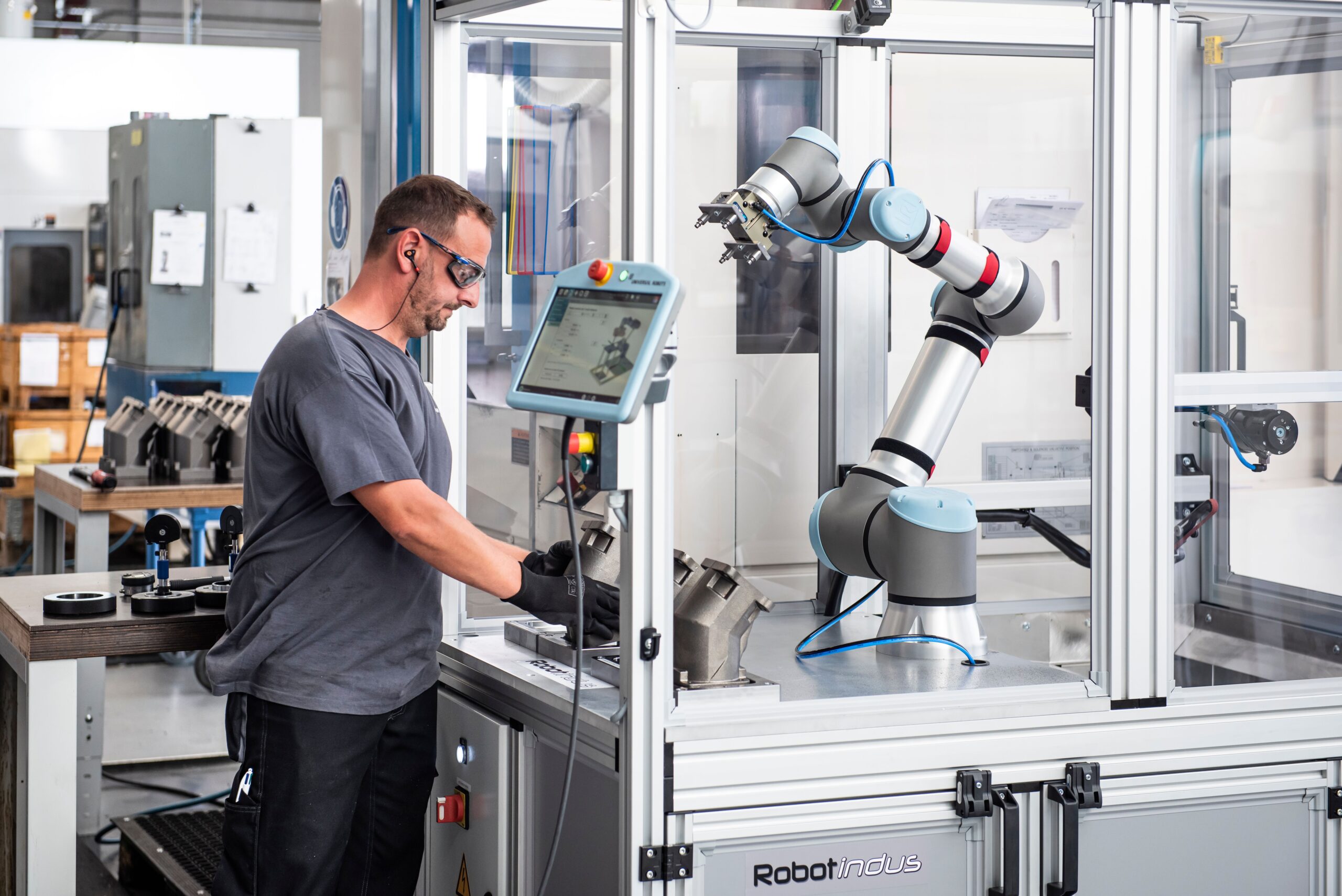
Complexity of integration
Integration with existing operational processes can be complex. For example, processes across the line might need to be set up differently. It might also require communicating with existing machines which can involve complex programming tasks. It is essential here to work with experienced integrators and suppliers who have expertise in robot implementation. This will minimize disruptions in daily operations.
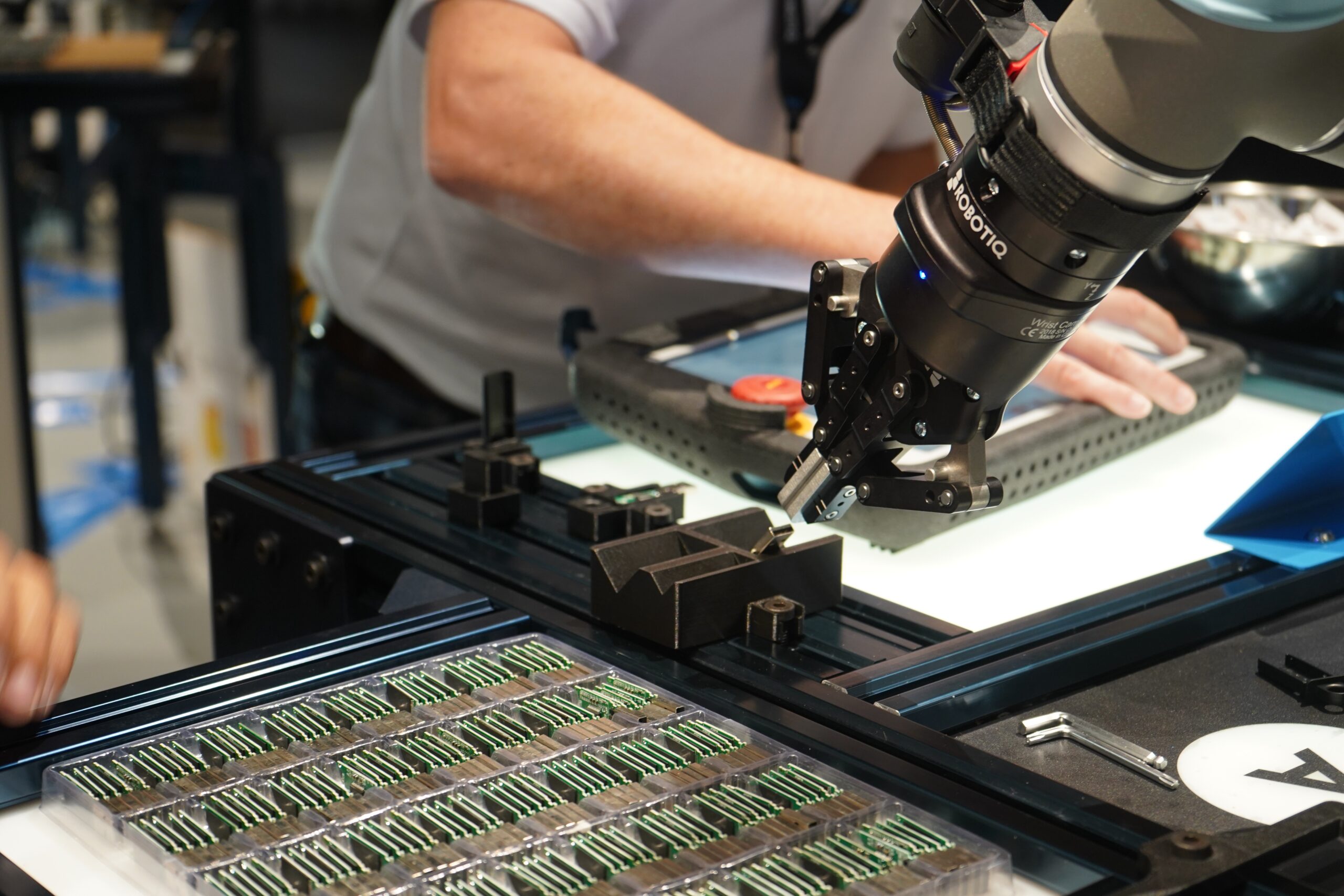
Change in work culture
The introduction of cobots may lead to changes in work structure and culture. Employees may have to get used to working alongside robots and be given new responsibilities. Open communication, training and staff involvement are crucial to reduce resistance and promote acceptance.
Tips for cobot implementation
Start small and scale up
Manufacturing companies would do well to start with small pilot projects to test the feasibility of cobot implementation. This allows potential challenges and optimizations to be identified in a controlled environment. If everything goes well and satisfactorily, it can be rolled out on a larger scale.
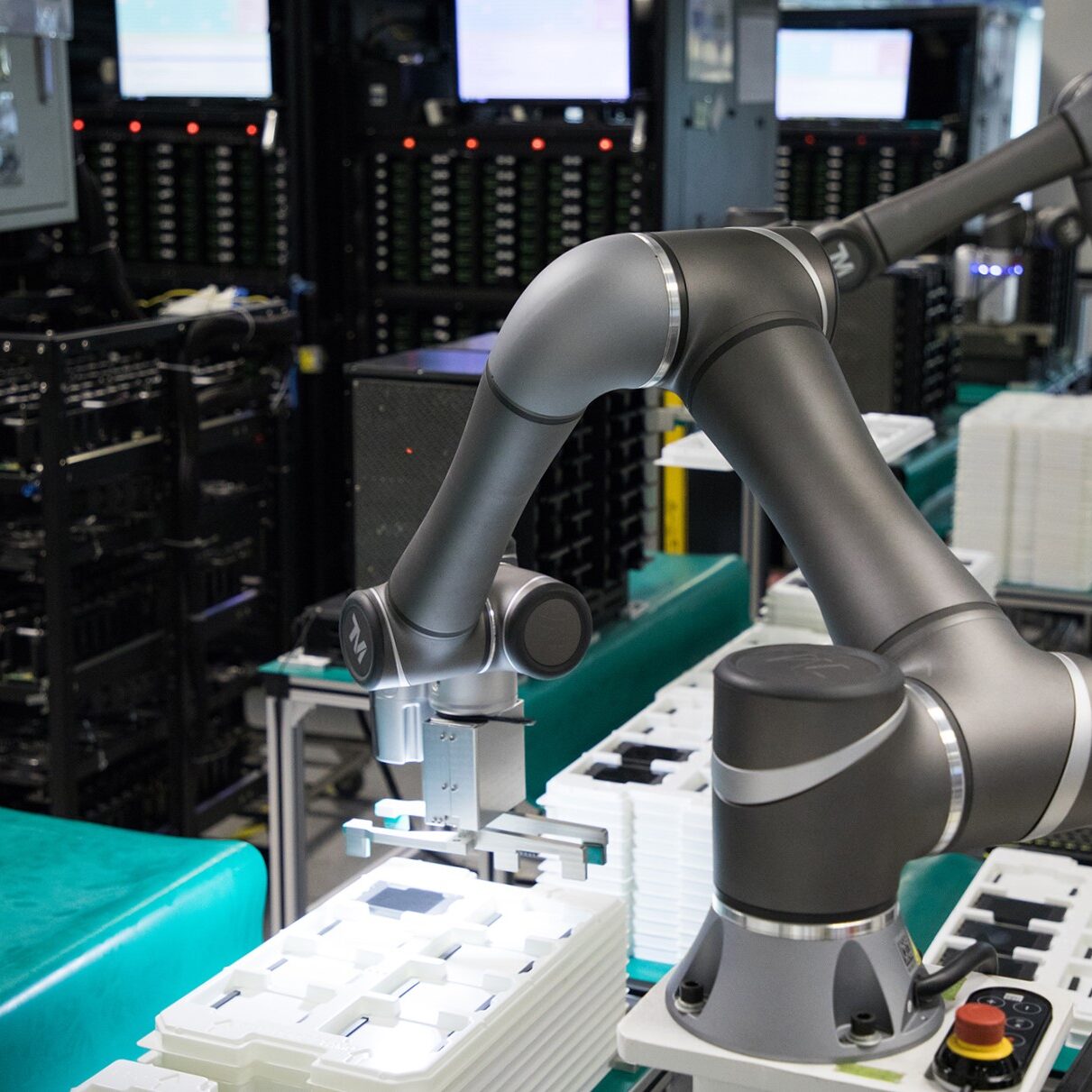
In-depth staff training
Training employees to work efficiently and safely with cobots is critical. This involves not only learning how to program the robots, but also understanding their capabilities and limitations. In addition, training and ongoing support help increase acceptance and productivity.
Flexible programmability
Thanks to user-friendly software, cobots are able to quickly adapt to changing needs and tasks. It is therefore wise for an implementation path to choose cobots with one with intuitive programming interfaces and the ability to perform different tasks. This increases the agility of the robot and minimizes the time for reprogramming.
Maintenance and data analysis
Cobots fit into the Smart Industry concept and thus are also capable of storing data. Monitoring the performance of cobots and analyzing this data are essential. Setting up a systematic maintenance plan and using data analysis tools allows users to predict failures and improve overall efficiency.
Getting to work!
Implementing collaborative robots offers companies significant benefits, but also comes with challenges. Understanding the lessons learned by other companies, as well as following best practices, is invaluable in successfully integrating cobots into an operational environment. By paying attention to safety, integration, training and flexibility, companies can harness the full potential of cobots and take their operational processes to new heights.
WiredWorkers is an expert in the field of automation and has already helped several companies implement collaborative robots. Contact us or schedule a free cobot consultation!
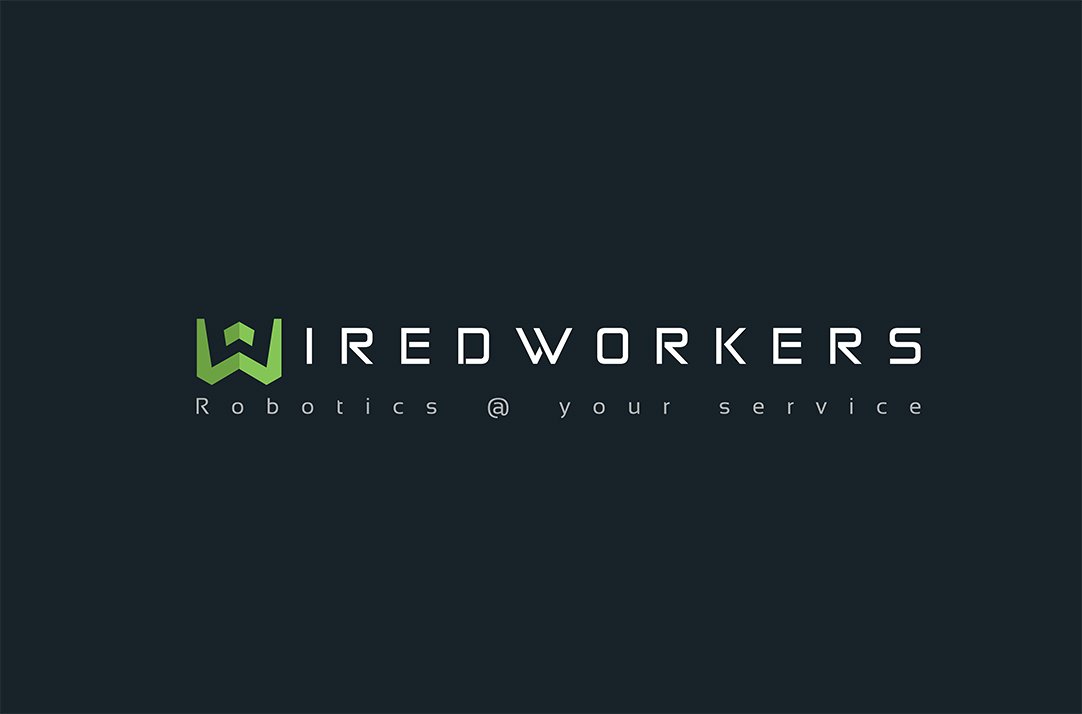