Several developments are increasing the demand for automation in the food industry. Worker safety, stricter food safety, increasing demand, and the need to increase productivity and reduce production costs are all factors that are forcing food manufacturers to develop themselves. Can cobots contribute to this?
The possibilities are increasing
Until recently, the food industry has benefited little from robotization, unlike, for example, the metal and electronics industries. Palletizing and packaging processes were successfully automated, but it was always difficult for robots to handle food products directly and in a delicate manner. Simply because foods have some unique characteristics that make them require gentle touch, or because they often have irregular shapes. Not to mention hygiene measures.
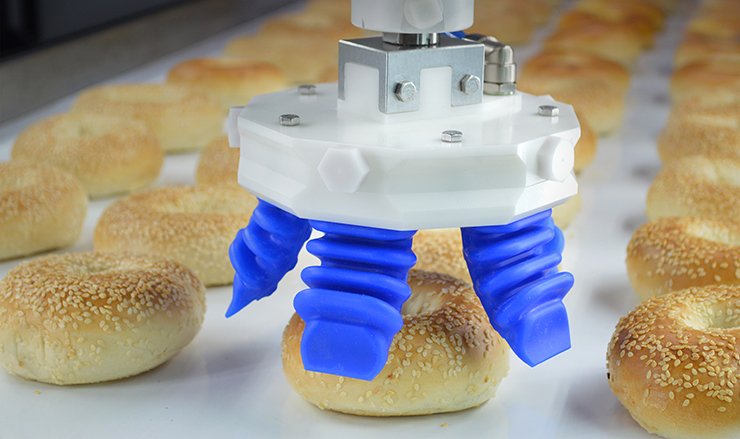
The introduction of new robotic and gripper technology combined with vision technology have changed the possibilities. For example, cobots and collaborative grippers are able to mimic human touch, vacuum grippers can perform packaging tasks with more sensitivity than traditional grippers, and soft grippers guarantee that products are not damaged.
The above developments have created more opportunities for food producers to automate. Think of picking and placing fruit or processing baked goods in bakeries. This has not gone unnoticed within the food sector either. Between 2014 and 2019, the number of manufacturers within that sector that have moved to automation has increased by 50%. So, what are the benefits of automation in the food industry and what should manufacturers consider when selecting food-related applications.
Employee safety and retention
To monitor worker safety, robots can take over tasks that are not safe or feasible for humans. In addition, robots can be a solution to retaining workers. If robots take over the boring and dirty tasks (from heavy lifting to repetitive pick-and-place operations), workers can perform more challenging tasks. Ultimately, this will lead to greater employee satisfaction.
Comply with food safety regulations
Legislative agencies are imposing increasingly stringent requirements on the food processing sector. When automating, it is therefore essential to choose certified grippers that are suitable for foodstuffs. In the US, FDA 21 CFR certification is looked at and in Europe, EC 1935/2004 certification is required for food handling. Certified soft grippers are recommended for handling delicate, fragile products. In addition, these grippers can more easily handle irregularly shaped objects such as fruits and vegetables. As for vacuum grippers, it is wise to use a gripper that does not require an external air supply. This prevents problems with dust, noise and reduces complexity.
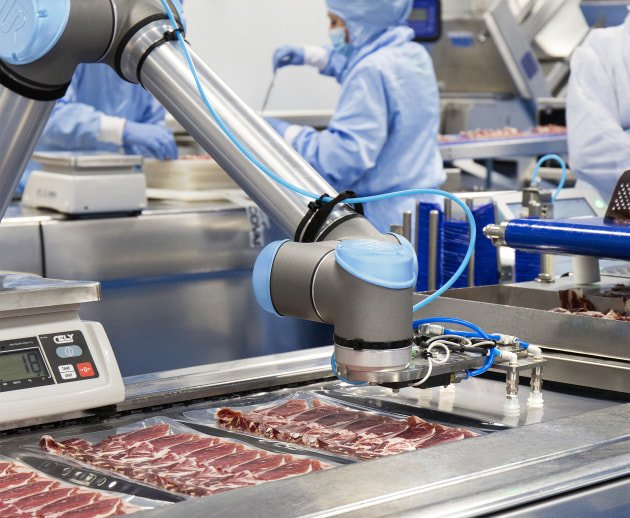
Factors to consider
When choosing a gripper, there are a few things to consider. First of all, the gripper must be able to handle the load capacity. Cleaning time is also important. Grippers that are dishwasher safe can reduce the overall cleaning time. In addition, it is helpful to look for grippers that can be easily changed. This reduces downtime for cleaning.
Along with cleaning and interchangeability, user-friendliness is also an important factor. Within the production sector there has been a shortage of skilled personnel for some time now. It is therefore important to choose automation solutions that are easy to operate by end users at all levels. Collaborative robots are a good example of this. These are specially designed to meet these characteristics.
Vacuum grippers or soft grippers?
So, in general, within the food industry, two types of grippers are most commonly used. The vacuum gripper and a soft gripper. But when to choose one, and when to choose the other? Soft grippers are perfect for fragile products that cannot be handled too hard, such as fruit. Also, these grippers are good for uneven surfaces. Vacuum grippers, on the other hand, are suitable for more robust tasks and require a smooth surface. This makes them great for things like cans, boxes and other packaging.
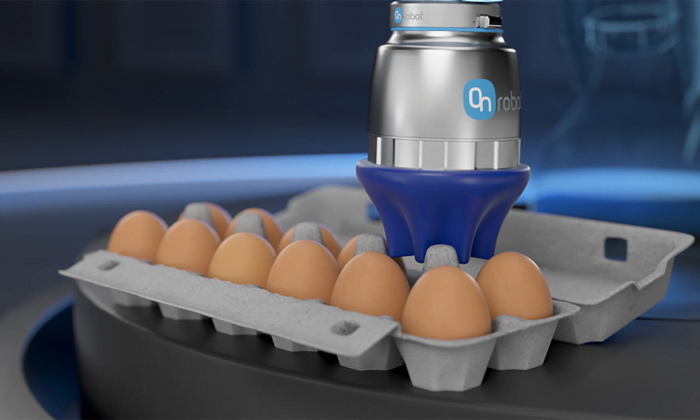
You could therefore generally say that a soft gripper leaves fewer marks on products and is therefore more suitable for the actual handling of food. Vacuum grippers are more suitable for the end of the production cycle when products are packed or stacked on pallets.
Get to work!
As mentioned, the demand for food will increase in the coming decades and the food industry will have to do its best to remain competitive. Robotization can help with this. Are you curious how cobots can contribute to improving your production process? Contact us or schedule a free cobot consultation.
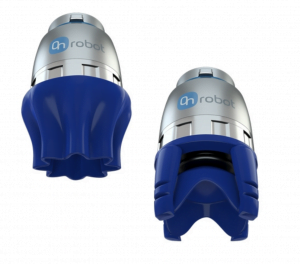