The safety of collaborative robots is a crucial aspect when implementing them in work environments where they work side by side with human operators. Various technologies and sensors are used to ensure that collaborative robots can work safely with humans. In this blog, we discuss some of these technologies how they contribute to the safety of these robots.
Force sensors: Controlling interaction forces
One of the key technologies used is the use of force sensors. Built into the robot's joints or grippers, these sensors are designed to measure the forces and torque applied when the robot comes into contact with an object or a person. By using these sensors, the robot can control and adjust the force with which it responds to external influences. For example, if the robot detects excessive force during an interaction, it can stop immediately to avoid injury.
Laser and radar scanners: Creating a safe perimeter
Laser and radar scanners are also commonly used to ensure the safety of collaborative robots in work environments. These scanners use laser beams or radio waves to create a detailed map of the robot's surroundings, continuously scanning for obstacles and changes in the environment. If an object or person enters a predefined safety zone, the robot can automatically slow down, stop, or alter its path to avoid a collision. Radar scanners are particularly effective in environments with dust, smoke, or poor lighting, where traditional vision sensors might struggle. By providing accurate, real-time data on the robot's surroundings, laser and radar scanners play a crucial role in maintaining a safe and efficient workspace for both humans and robots.
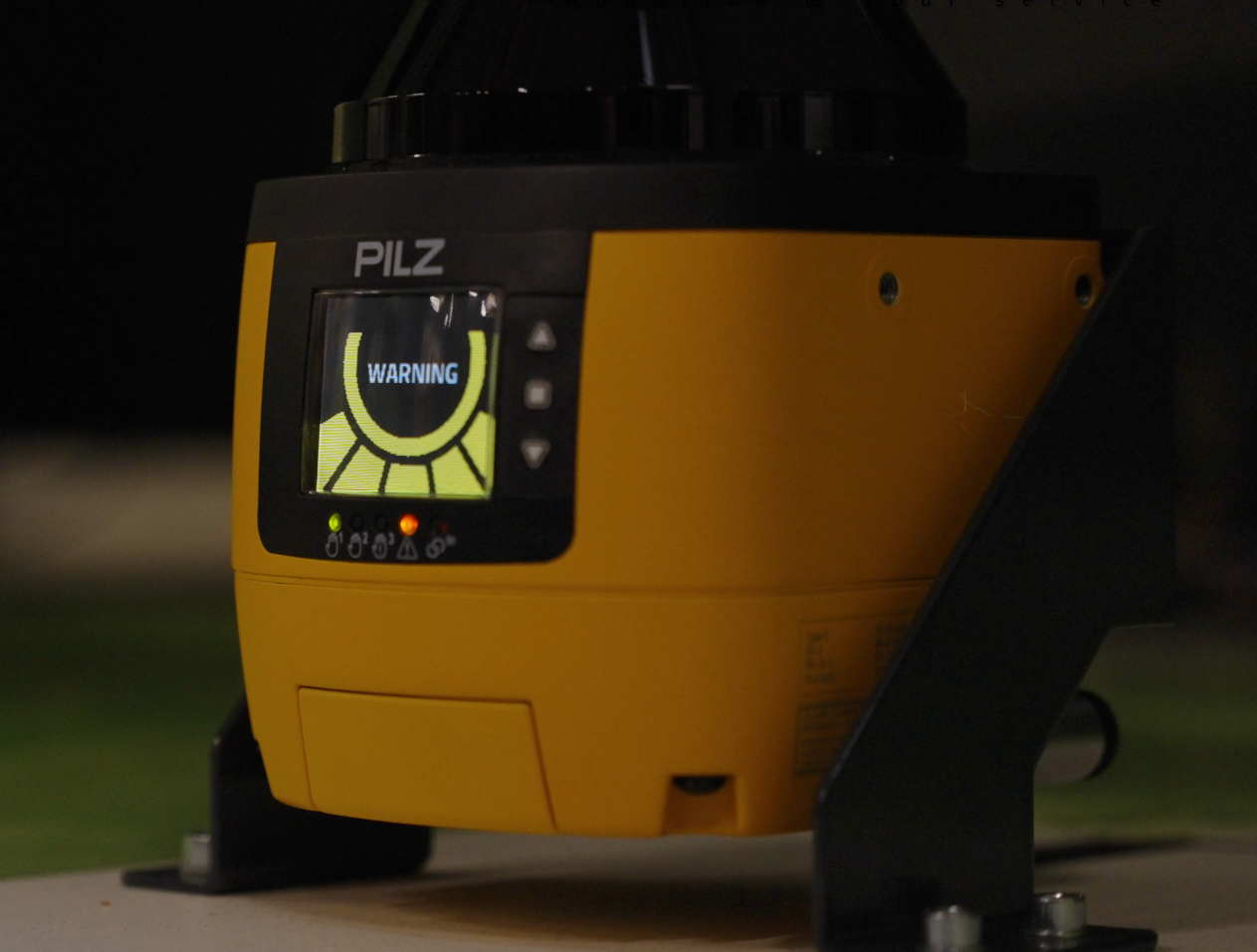
Presence sensors: Responding to proximity
Another important technology used is the presence sensor or proximity sensor. These sensors detect the presence of a person or object in the robot's immediate vicinity. They use various technologies, such as ultrasonic, infrared or lasers, to measure the distance to objects. When the sensor detects a proximity, the robot can react immediately by reducing its speed, stopping its movement or adjusting its trajectory. This helps prevent collisions and injuries.
Safety stop buttons: Immediate emergency stop
Safety stop buttons are another essential component of collaborative robot safety. Strategically placed in the work environment, these buttons allow operators to immediately stop the robot in the event of an emergency. Pressing the button immediately shuts down the robot and prevents further movements or actions that could be dangerous. This provides an additional layer of security and peace of mind for human operators.
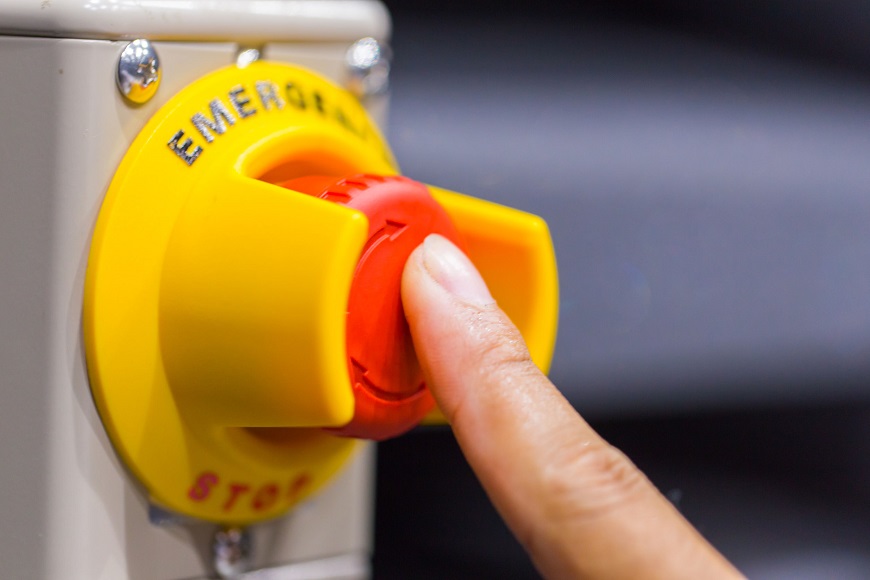
Safety fences and enclosures: Physical separation between humans and robots
Safety barriers and fences create a clear separation between human operators and the robot work environment. These barriers prevent direct physical contact between humans and robots, minimizing the risk of injury. Access to the robot zone is restricted through doors that can only be opened using safety systems, such as electronic locks or sensors that detect when no humans are present within the robot zone. This ensures that the robot is active only when there is no direct interaction with human operators.
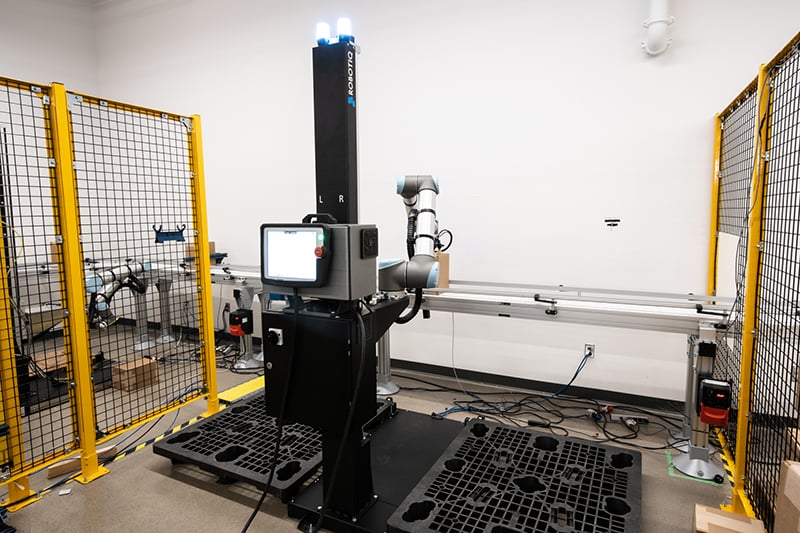
Standards and guidelines for safety
In addition to these technologies, standards and guidelines have been established to ensure the safety of collaborative robots. Organizations such as the International Organization for Standardization (ISO) have established standards, such as ISO 10218 and ISO/TS 15066, that provide guidelines for the design and implementation of collaborative robotic systems. Among other things, these standards describe requirements for safety functions, such as speed limits, force and torque limits, and assessments of the risks and hazards associated with the use of collaborative robots.
Training and awareness: cooperation between man and machine
It is important to note that although these technologies and safety measures reduce risks, human-machine collaboration still requires careful planning and monitoring. Training and informing human operators about safety procedures and the proper use of collaborative robots is essential to prevent accidents.
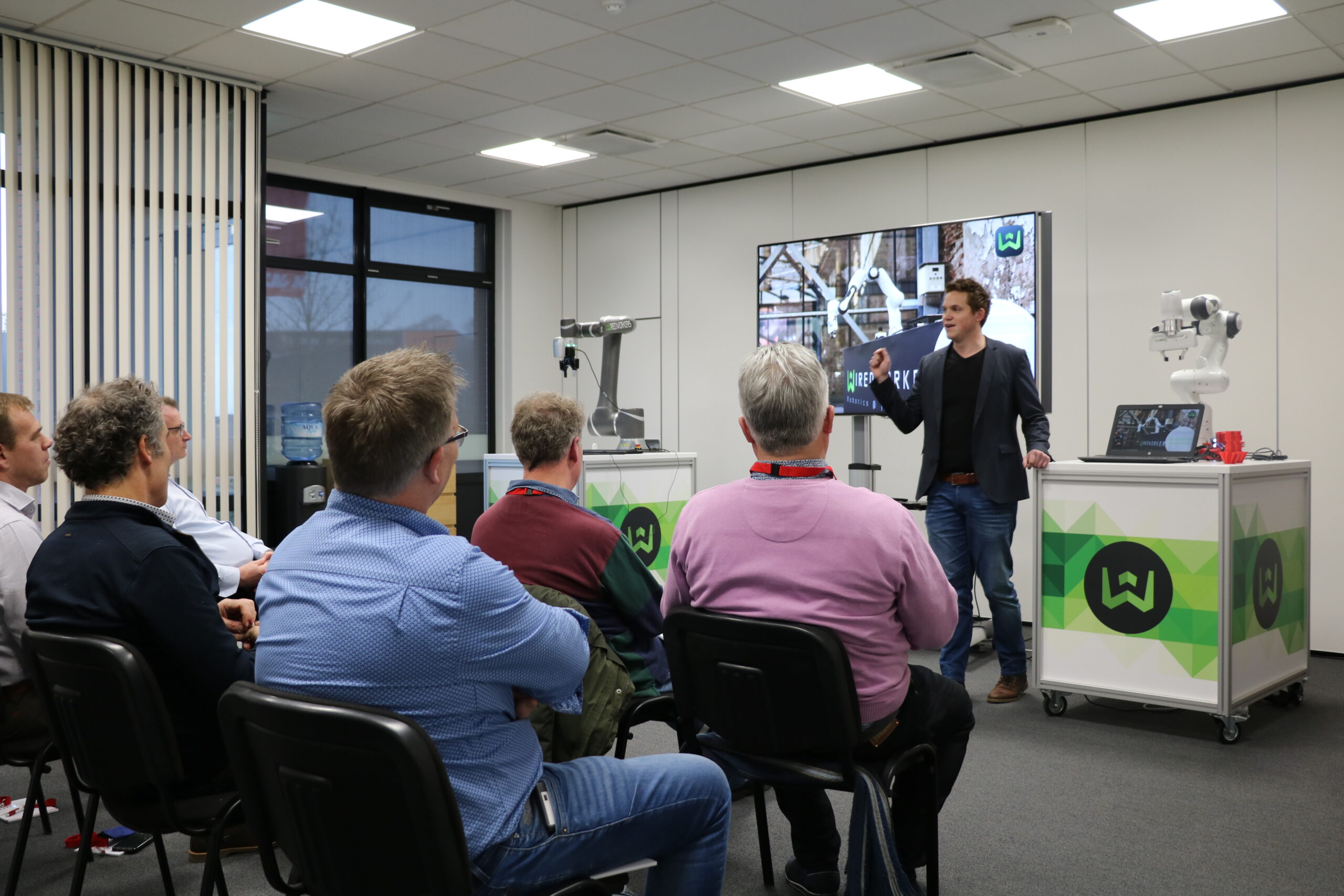
Getting to work!
In other words, various technologies and sensors, such as force sensors, vision sensors, presence sensors and safety stop buttons, along with safety gates and enclosures, ensure the safety of collaborative robots. These technologies help detect obstacles, measure forces and torques, reduce speeds and stop movements to prevent injuries. In addition, there are standards and guidelines that regulate and recommend safety aspects of collaborative robot systems.
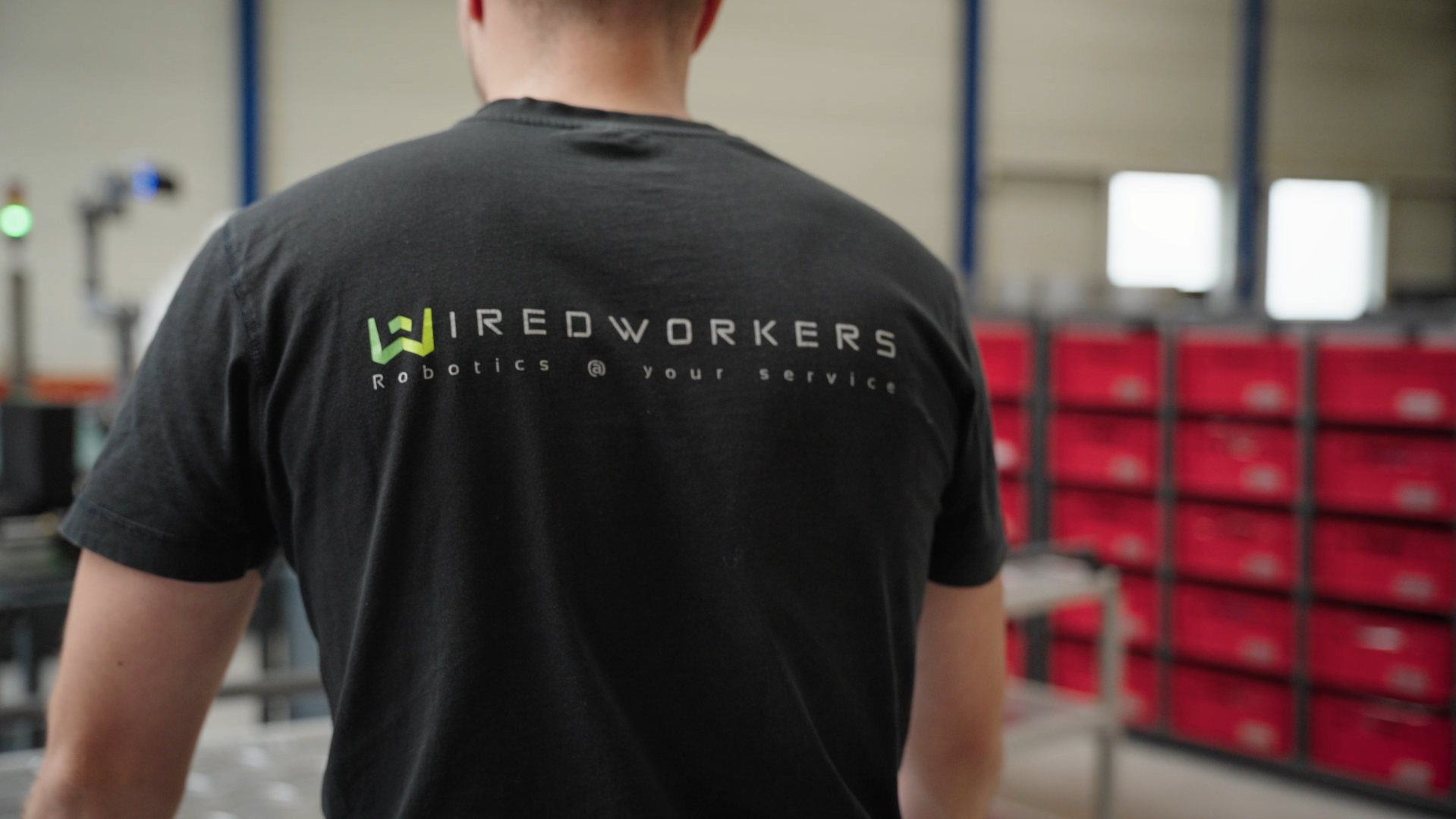
WiredWorkers has experience implementing cobots and can advise on the proper use of these technologies and following safety procedures. In addition, we offer cobot training to safely implement human-cobot collaboration in manufacturing environments. Contact us or schedule a free online consultation.