Automated PCB Testing
The assembled circuit boards, which form the basis of each product to be developed, must meet strict quality standards. Various inspection and testing methods are applied during the production process.
One of the methods used by H&F Electronics to ensure flawless delivery of printed circuit boards is the pinbed test. This involves placing the PCB on a pinbed, where the pins come into contact with various test points to assess the quality of the PCB through a functional test. WiredWorkers has developed an automated test setup specifically for this pinbed test.
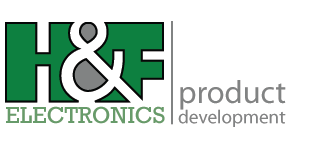
Full trays of approved PCBs
To feed the robot, roller conveyors were placed on the side of the machine. Stacks of trays containing the circuit boards are placed on these. There are also two trays placed inside the machine on a jig. One to hold rejected PCBs and one that acts as a buffer. When a PCB is rejected, a PCB is removed from the buffer to ensure that full trays of approved PCBs always come out of the machine. Using a vacuum cup, it picks up the PCB and places it in a mold. This serves as a precise orientation for picking up and placing the PCB in the test machine. The circuit board is then placed in the testing machine and the robot closes the lid of the testing device. Meanwhile, a new circuit board is placed in the mold. Once the circuit board is approved, it first passes a printer that prints a data matrix on it and is then placed in the designated tray. Vision is used to orient where the circuit board should be placed in the tray. Using this vision eliminates the need for additional alignment tooling. When a tray is empty, it is picked up and placed over the full tray of approved PCBs. In this way, full trays of approved PCBs are eventually delivered. Watch the video below.
Increased productivity and employee satisfaction
Workers previously tasked with manually placing printed circuit boards into test machines now have the opportunity to focus on higher-impact tasks. This change has not only freed them from the monotonous task of manually testing large batches, but also allows them to engage in more complex responsibilities, such as fault analysis. As a result, this shift in tasks has contributed to increased employee well-being and satisfaction.
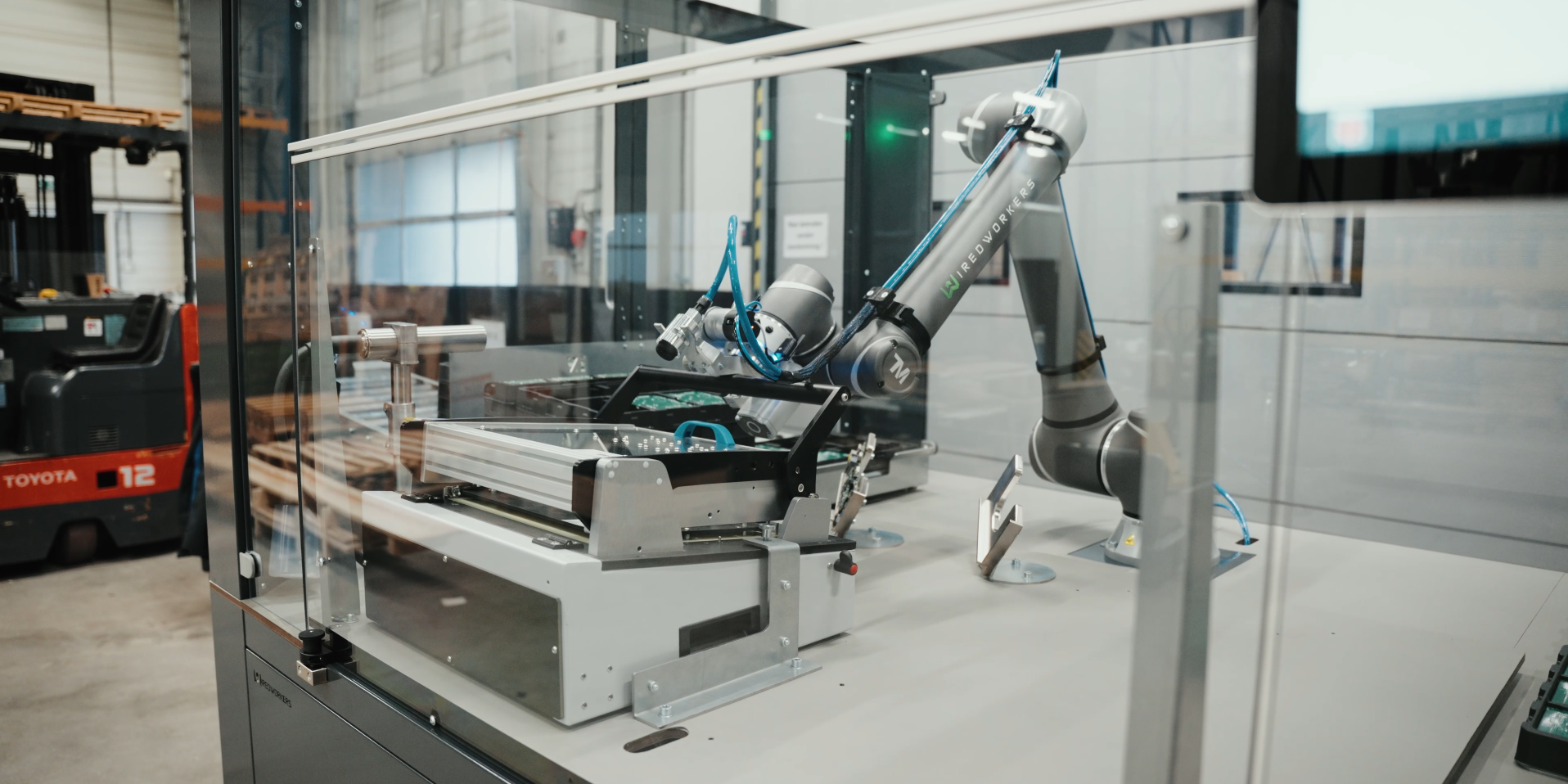