What types of palletizers are there and what are they suitable for?
If manually stacking bags, boxes or other materials is asking too much of the staff, it's a good idea to look at a way to automate that. There are many different ways to do this, but the most obvious one is a palletizer. Nevertheless, palletizer is a broad term and there are different types of palletizers that all perform slightly differently. Therefore, in this blog we will take a look at different palletizers and see what they are best suited for.
Different types of palletizers
Palletizers and pallet configuration are crucial in many different industries, from manufacturing to warehouse management and from logistics to distribution. Choosing the right palletizer system can have a significant impact on a company's productivity, cost effectiveness and overall operations. There are three types of palletizers that all have their unique characteristics and applications, namely; industrial palletizers, collaborative palletizers and conventional palletizers.
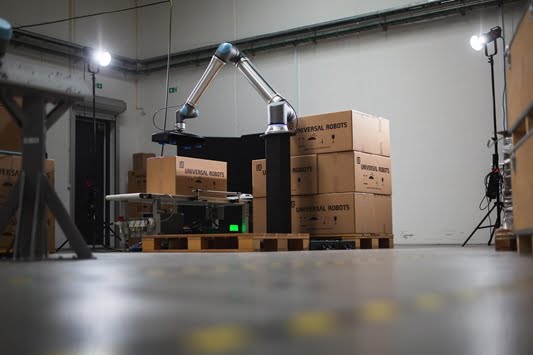
Industrial palletizers
Industrial palletizers are robotic systems set up to handle heavy materials at high speeds. They are designed to provide compact palletizing without high maintenance. Ideal for high-throughput industries. Here are some key features and applications.
Stacks cases, bags, bottles and cans.
Lift up to 180 kg at a time and stack faster.
Build stacks up to 250 cm tall with longer reaching arms.
Smart configurations allow any number of lines or pallets to be built simultaneously.
Material handling options available for pallets and sheets.
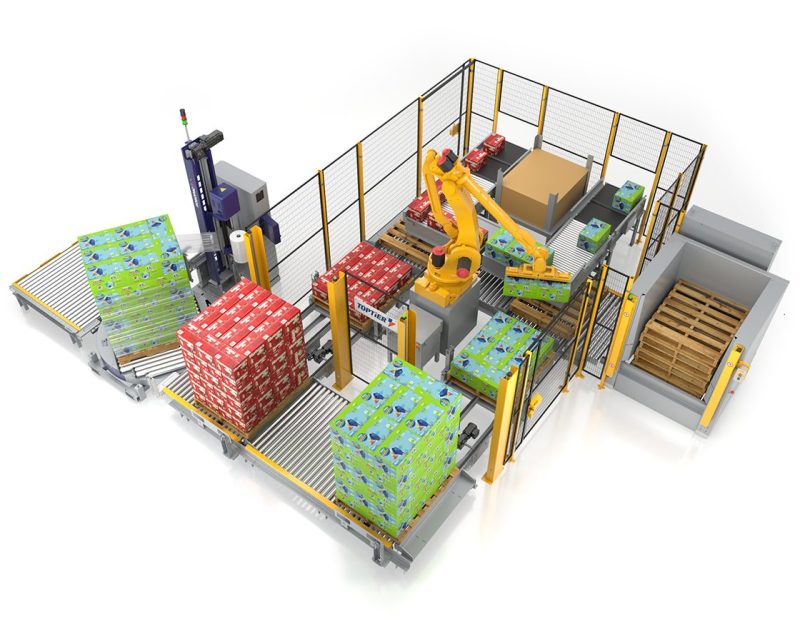
Speed and precision
One of the features of industrial palletizers is their impressive speed and precision. This allows them to stack products at lightning speed and very precisely according to the ideal pallet configuration. This makes them suitable for high-volume production lines.
Space efficiency
These palletizers, relatively speaking, don't take up that much space, keeping the floor space of the factory or warehouse at its best.
Heavy load
Industrial palletizers have higher payloads making them suitable for industries where products are relatively heavy.
Double line stacking
Many industrial palletizers can stack products coming from two different supply lines. This gives their efficiency a huge boost.
Applications of industrial palletizers
Industrial palletizers are widely used in industries such as, food processing and manufacturing, where the demand for fast stacking and material handling is critical.
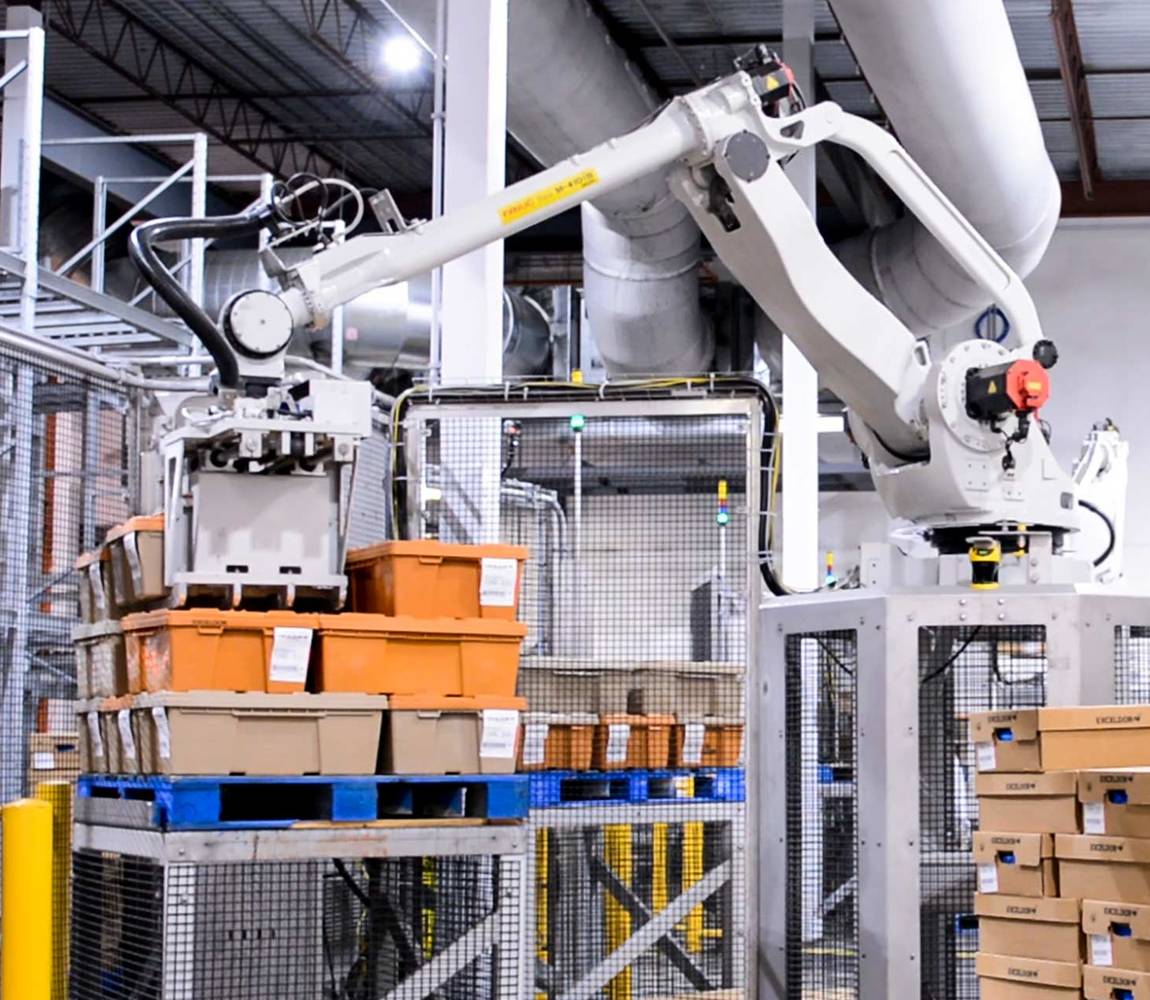
Collaborative palletizers
Collaborative palletizers, or cobot palletizers, take a different approach to the process. Cobots are robots that can collaborate with humans because they are equipped with sensors that make them feel, so to speak. As a result, they will stop working if they are obstructed in their path. Cobot palletizers are therefore aimed at human-robot cooperation, thus involving humans more in the process. Although they do not match the speed of industrial palletizers, cobot palletizers have their own advantages, especially in terms of flexibility and cost-effectiveness. Here's what you need to know about collaborative palletizers.
Features collaborative robot arm.
Advanced safety allows Human-in-the-Loop workflows.
Lift cases weighing up to 25 kg.
Stack pallets up to 3 meter
Capable of handling slip sheets
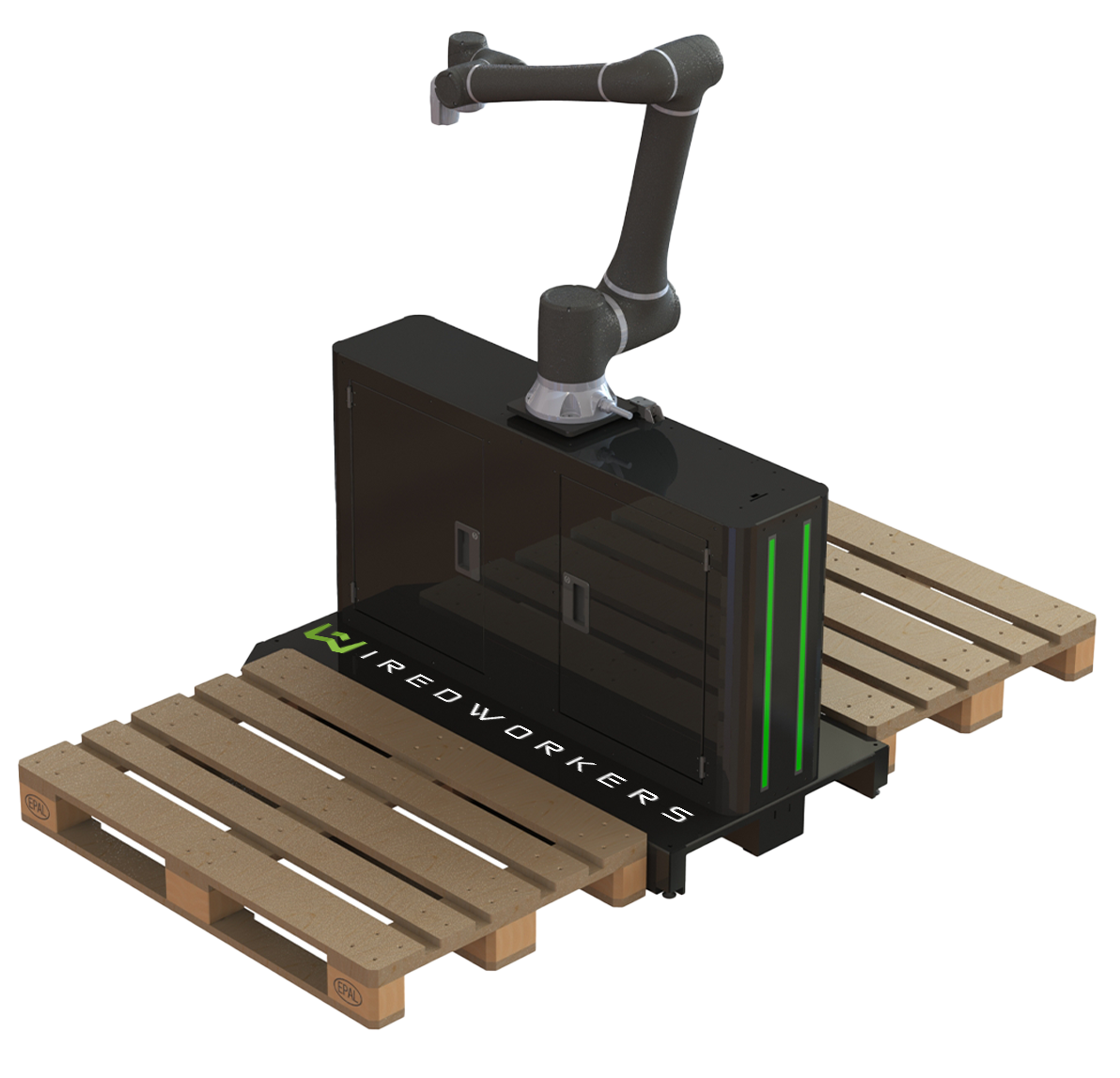
Human-in-the-Loop
Collaborative palletizers involve human workers in the stacking process. Workers can place sheets and load pallets alongside the robot, creating a more flexible and adaptable palletizing process that adapts to desired pallet configurations.
Stacking boxes
Cobot palletizers are usually used for stacking boxes or crates. In addition, they are also capable of placing slipsheets between layers.
Flexibility
Collaborative palletizers are equipped with user-friendly software. This allows them to be easily reprogrammed for different tasks, making them ideal for operations that require frequent changes in production lines and pallet configurations.
Applications of cobot palletizers
Cobot palletizers are widely used in industries where speed is not the main concern, such as smaller manufacturing plants, warehouses and distribution centers or in places where there is a lot of variation in production that requires a palletizer process to be converted frequently.
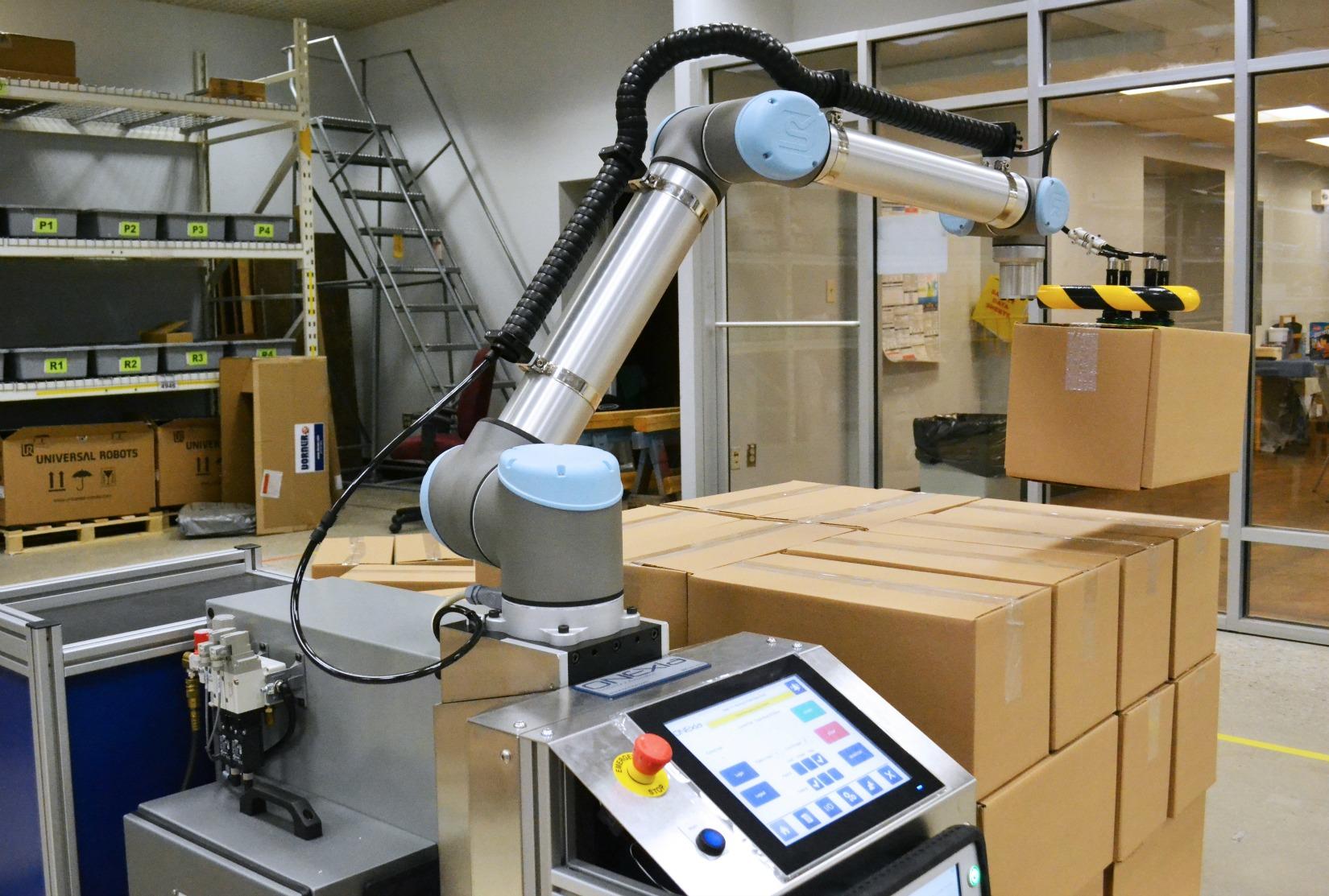
Conventional palletizers
Unlike robotic systems, conventional palletizers rely on mechanical pushers and overhead gantries to arrange products in specific patterns for stacking. These systems often require more space, but have their own unique capabilities.
High-speed case and bag palletizing, up to 60 units per minute.
Low-level and high-level options available.
Automatic pallet and sheet handling.
Concurrent stretch wrapping options help stack unsteady loads.
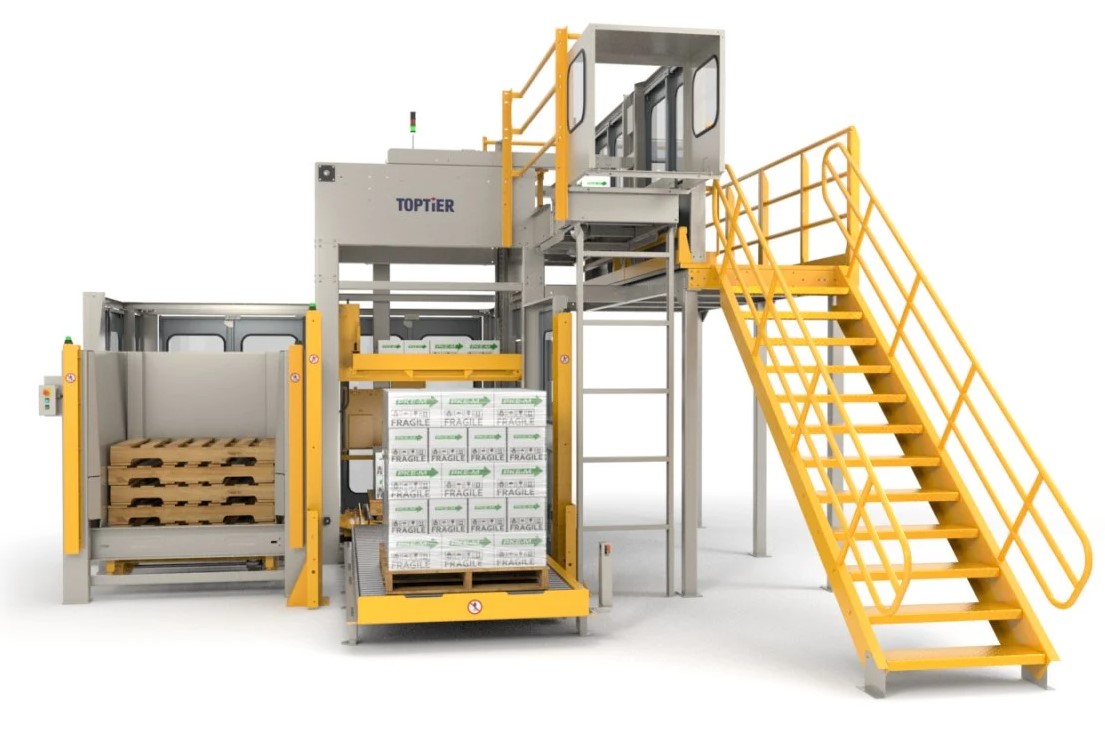
Pattern-based stacking
Conventional palletizers are excellent at arranging products in specific patterns, which is crucial in industries where pallet configuration and stability of stacked products are important.
Stretch wrapping
Some conventional palletizers can incorporate stretch wrapping capabilities, further automating the palletizing and packaging process in one place.
Space requirement
Conventional palletizers generally have greater space requirements compared to robotic systems, making them more suitable for larger plants with adequate floor space.
Applications of conventional palletizers
Industries that rely on conventional palletizers include those that deal with bags, bulk items and products that require complex stacking configurations.
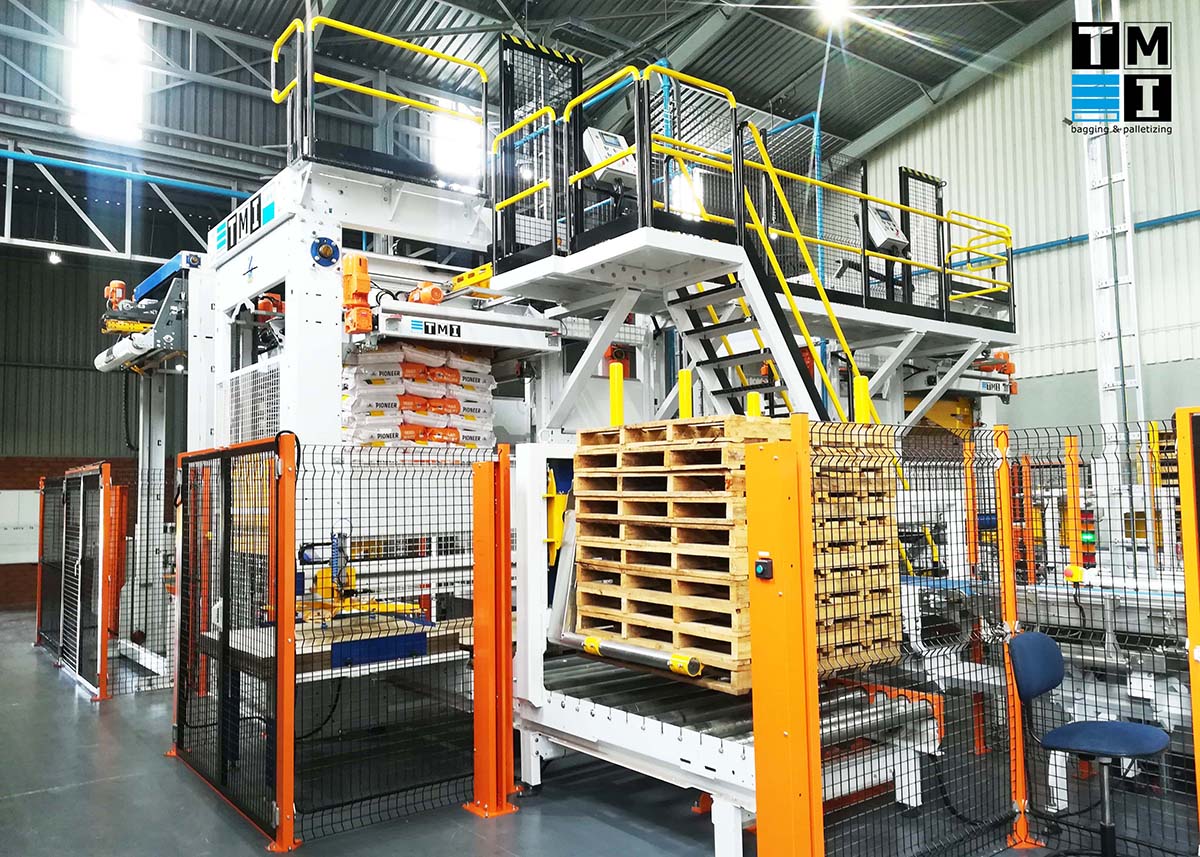
Conclusion
Choosing a palletizer depends largely on the specific needs of a business or industry. Industrial palletizers are the solution for fast, heavy load operations, while collaborative palletizers offer flexibility and cost effectiveness. Conventional palletizers are ideal for company that prioritize precision in stacking patterns and have the ability to use more floor space.
WiredWorkers is an expert in automation and has already helped several companies implement palletisers. We can help design an efficient robot cell, including a clear cost estimate and ROI. Contact us or schedule a free online consultation!
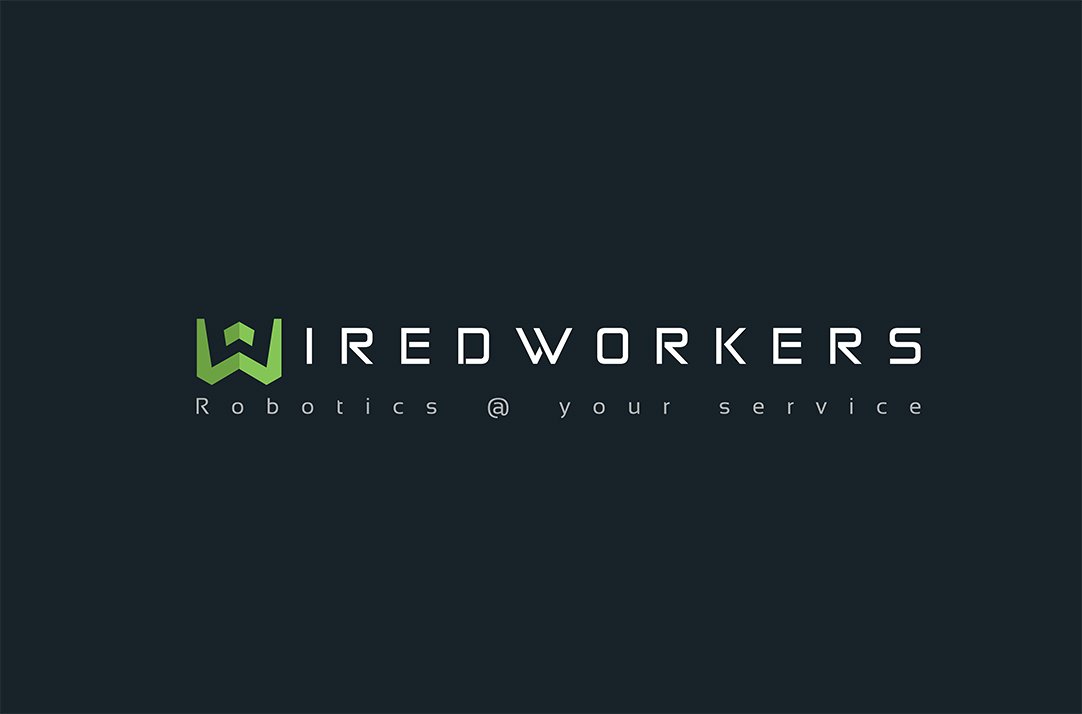
Frequently Asked Questions
What are the main differences between industrial, collaborative and conventional palletisers?
The main differences between industrial, collaborative and conventional palletisers are that industrial palletisers are optimised for high speed and precision when handling heavy materials, collaborative palletisers are designed to work with human workers and offer flexibility and cost-effectiveness, while conventional palletisers rely on mechanical pushers and overhead gantries to arrange products in specific patterns, which is ideal for industries where precision in stacking patterns is a priority.